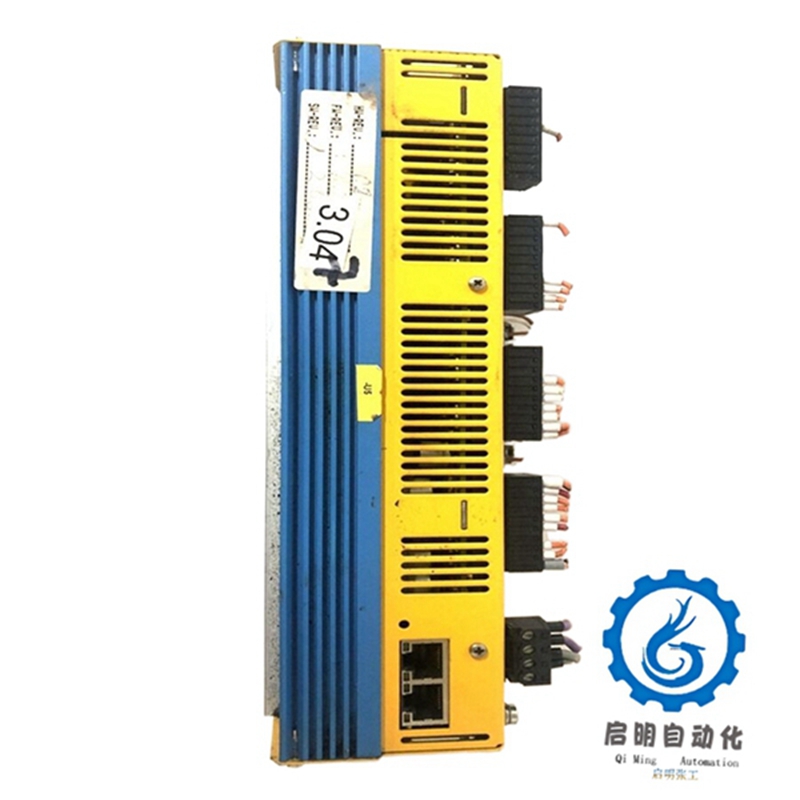
05704-A-0121 Electromechanical actuators require intelligent integrated driver solutions to enhance edge intelligence
05704-A-0121
introduction
In the process of seeking to enhance edge intelligence, physical edge devices such as electromechanical actuators require more intelligence in order to gain advantages such as better real-time machine decision-making. These actuators provide intelligent, valuable, and rich sensor based feedback. This type of edge device is crucial for Industry 4.0 and higher stages. They control robots, manipulate factory processes and automate them, convert digital information into physical motion, and provide high-level intelligence and self-awareness. When the actuator manipulates an object, the sensor is used to measure and quantify actual parameters, and convert physical values back to digital values. Therefore, actuators and sensors are still considered different devices or components in most cases.
Stepper motors and solenoid valves occupy a large part of these electromechanical actuators, which can be seen in every factory workshop, various automotive applications, laboratory automation, and other occasions. Driven by laboratory and medical applications, industrial applications, and automotive applications, the global market for stepper motors and solenoid valves has reached billions of dollars and is constantly growing. These applications require increasing automation and miniaturization of electronic devices for actuators and drivers. Traditional drive solutions cannot meet these new requirements and lack detection capabilities.
A brand new silicon cDriver ™ The solution consists of intelligent controllers and drivers, which integrate sensor and actuator functions into a single integrated component for use within embedded motion control solutions, enabling edge intelligent actuators 2,3. For system parameters and state variables that can only be directly obtained from electromechanical actuators, they can be measured and evaluated on-site (such as temperature, solenoid valve response time, and motor load values).
The fusion of sensor functions and actuators has changed the paradigm of electromechanical actuators. They have evolved from simple power conversion systems to self-awareness sensors that can effectively control actuators and provide in situ feedback data to higher control levels, cloud or AI productivity solutions. The electromechanical unit has become a sensor.
Electromechanical actuators – Overview
Stepper motors and solenoid valves are widely used in the fields of automobiles, industry, and healthcare. There are many similarities between the two: the copper wire coil causes mechanical movement when energized.
A two-phase stepper motor is usually controlled by two current sources, which induce 90 ° phase shifted sine and cosine shaped currents in the two phases of the stepper motor. The current flowing through the stepper motor coil (stator) determines the direction of the magnetic field. The rotor is oriented like a compass in the magnetic field of the stator coil. By electrically controlling the rotation of the magnetic field, the rotor can rotate through orientation in the magnetic field. Figure 1 shows the stator/rotor arrangement of a standard hybrid stepper motor and some examples of different types of stepper motors.